Anti-cut gloves are necessary protective equipment for practitioners in manufacturing industries such as clothing production, meat processing plants and machinery and equipment manufacturing, metallurgical industry, engineering construction, laminated glass, metal sheet production and processing, etc. They are also ideal for petrochemical equipment, smelting plant mining, and meat cutting. Labor protection supplies for manufacturing industries such as laser cutting and processing of metal materials, disaster relief and disaster relief.
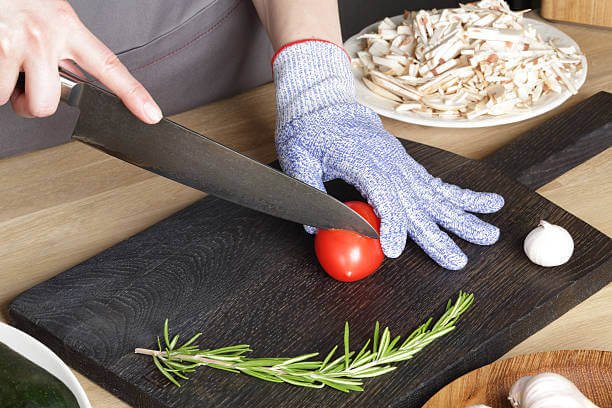
At present, the common anti-cut gloves on the market are basically divided into anti-cut gloves made of stainless steel plate gloves, HPPE gloves, steel wire gloves, Kevlar gloves and other materials. The service life of a pair of anti-cut gloves is equivalent to 500 pairs of ordinary wire gloves. It has incomparable features. Cut resistance and abrasion resistance.
Stainless steel plate gloves
Wire gloves are made of tiny rings of stainless steel plates connected to each other. Its characteristic is that it has the highest level of anti-cutting and can withstand the risks of some strong laser cutting forces, but the disadvantage is that it is too heavy and expensive.
HPPE gloves
HPPE gloves have different levels of cut resistance. Generally, these gloves are divided into three levels and five levels. Level 5 general gloves need to add additional glass fiber to truly achieve level 5, but the glass fiber is easy to break and the performance is not very good. HPPE gloves with palms dipped in PU glue are more common.
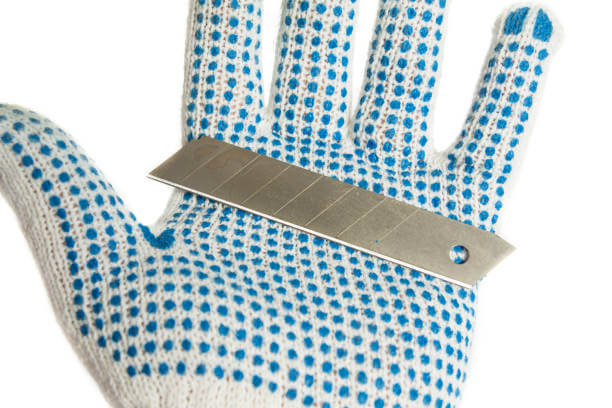
Wire gloves
What plays an important role in steel wire gloves is the fine stainless steel wire component, which is usually made into covered yarn and then woven into gloves. This glove is on the stiff side.
Kevlar gloves
Kevlar gloves are protective gloves woven from Kevlar cotton yarn with patented technology produced by DuPont in the United States. They are most commonly seen in light yellow, and each glove contains the Kevlar trademark logo. This glove is not only cut-proof but also insulating and heat-insulating, but it is very easy to fade when exposed to the air. Kevlar gloves are further processed into palm covers, palm lifts or palm filaments. They all increase the life of your gloves.
Classification of anti-cut gloves
In fact, China has already had specific specifications to define the level of cut-resistant gloves, which are required in the national standard GB24541-2009 Arm Safety Protection Mechanical Equipment Injury Protective Gloves Standard. However, Chinese cut-proof glove manufacturers still promote their own gloves in accordance with EU policies and regulations, which actually does not comply with the regulations.
Both China’s specifications and the policies and regulations of EU countries divide the anti-cut level of anti-cut gloves into five levels. Before purchasing this type of protective gloves, consumers should first determine which level of cut-resistant gloves they need to avoid blindly following the trend.
The broader cut-resistant specification for cut-resistant gloves is the British EU BS EN388 (equivalent to the Australian/British specification AS/NZS 2161.3). Specifications include four types of reflective risks, namely anti-corrosion, anti-cut, anti-tear and anti-puncture. Cut-resistant gloves that meet the specifications must be marked with a shield symbol in the image of a blacksmith’s hammer, and the protection level is expressed from 1 to 4, with the cut-resistant rating reaching the maximum level 5.
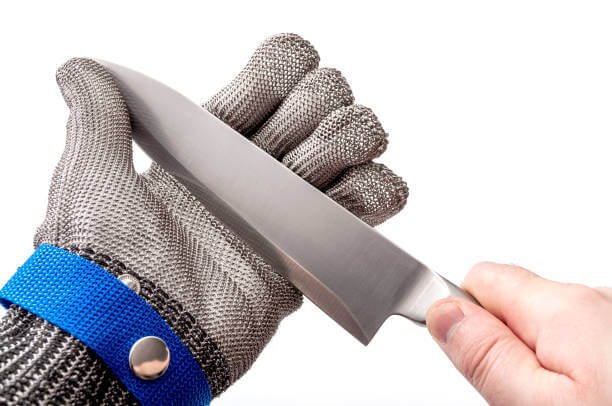
In some cases “x” and “0” are also used, each indicating unsuitability and a rating less than “1”. Cut-resistant gloves must also comply with the general, comfortable and efficient, test procedures and labeling and material requirements of the BS EN420 specification, such as related water penetration, the amount of hexavalent chromium released by cloth gloves, etc.
As a special labor protection product, when carrying out anti-cut testing, a sample is taken from the palm of the glove, a tungsten steel material is used to turn the cutting knife back and forth for cross-cutting, and the speed required to cut through the sample is recorded to compare the overlap at the same time. According to the results of the standard pure cotton fabric sample for verification and testing, the higher the index value calculated, the stronger the anti-cut performance. However, anti-cut detection discomfort is used for very hard materials.